Jest to jedno z pytań najczęściej niezadawanych na obronach prac dyplomowych na Wydziale Mechanicznym Technologicznym Politechniki Warszawskiej. Dlaczego? Cóż, świadomy tematu i sprytny dyplomant może niczym nasza ukochana tenisistka z czołówki rankingu WTA, szybko „odbić piłkę” egzaminatorowi pytaniem gdzie? lub kiedy?.
Kiedy – kilka słów na temat historii wytwarzania form
Jeszcze niecałe 100 lat temu, w czasach bakelitowych popielniczek i „kontaktów” każda forma prasownicza i wtryskowa była niemalże unikatowa. Co zakład, co konstruktor to inny pomysł na ustalenie połówek formy, mechanizm wypychania wypraski itd. Wytwarzanie form było zatem zawsze niemalże w 100% jednostkową produkcją, czyli najmniej wydajną z możliwych.
Rosnące zapotrzebowanie na wtryskiwane elementy z tworzyw polimerowych (już nie tylko z bakelitu) wymagało wyższych wydajności w wytwarzaniu form wtryskowych i ich projektowaniu. Odpowiedzią na te wymogi okazał się opatentowany przez firmę HASCO w 1960 roku modułowy system budowy formy. Od tamtej pory każda forma wyglądała jak „skrzynka Hasco” i w większości składała się z produkowanych seryjnie części znormalizowanych. Rozpoczęła się era narzędzi „składanych klocków”, a w projektowaniu form (paradoksalnie) forma przestała przysłaniać treść, czyli funkcję odwzorowania kształtu gniazda przez tworzywo. Sytuację tę pogłębiło wprowadzenie na rynek w latach osiemdziesiątych ubiegłego wieku dedykowanych do konstrukcji form systemów CAD, takich jak Cimatron (1982 r., wtedy pod nazwą MicroCAD), w których znajdowały się już biblioteki znormalizowanych części HASCO. Teraz w zasadzie jedyną rzeczą wymagającą prawdziwie inżynierskiego zaangażowania stało się gniazdo formy. Resztę elementów składowych projektowanego narzędzia program CAD wstawia prawie że automatycznie.
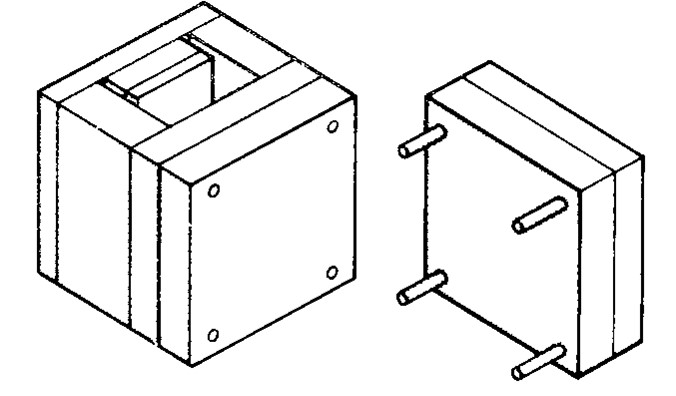
Rysunek 1 Standardowa „skrzynka” HASCO [1]
Mniej więcej w tym samym czasie na rynku zaczęły pojawiać się programy do symulacji przepływu tworzyw w formie (Moldflow 1978 r., Moldex 1983 r.). Oznaczało to, że nie tylko nie było już potrzeby ręcznego opracowywania geometrii poszczególnych część składowych narzędzia (kreślenia), ale też ręcznego prowadzenia koniecznych przy konstrukcji from obliczeń, takich jak spadek ciśnienia tworzywa na drodze płynięcia, czy wydajność układu chłodzenia. Dodatkowo pojawiły się możliwości prowadzenia analiz, których wcześniej po prostu nie dało się wykonać, np. określenie możliwych wypaczeń wypraski.
Obecnie jest możliwa, choć w dalszym ciągu jednostkowa produkcja form wtryskowych z wydajnościami typowymi dla wytwarzania masowego. „Chińskie fabryki form” są w stanie m.in. dzięki wykorzystaniu technik wspomagania komputerowego produkować tysiące form wtryskowych rocznie.
Gdzie – szukać informacji na temat nauki podstaw budowy form wtryskowych
W 2024 roku nadal jednym z podstawowych materiałów dydaktycznych do nauki podstaw budowy form wtryskowych jest podręcznik „Konstrukcja form wtryskowych do tworzyw termoplastycznych” autorstwa Henryka Zawistowskiego i Daniela Frenklera z 1984 r. W przedruku tej książki wydanym w 2003 r. do rysunku schematu przebiegu uruchamiana produkcji nowej wypraski w rozdziale „Zasady projektowania form” autorzy dodali przypis: „Schemat już nieaktualny – nie uwzględnia technik CAD/CAM/CAE”. Do tegoż przypisu, dodałbym uwagę, że nie wszędzie uwzględnia się ww.. techniki. Mam tu na myśli przede wszystkim symulacje wtrysku, czyli CAE, bo na szczęście nikt już poza biednymi (z tego powodu) studentami na papierze nic nie kreśli. Można by spytać dlaczego w kraju nad Wisłą, w już wcale nie tak zacofanej części Europy dalej „jedzie się po schemacie” sprzed czterdziestu lat? Do kopania grządek na działce to nawet wynaleziony 5 tysięcy lat temu szpadel wystarczy, ale do „seryjnego” kopania rowów trzeba już koparkę odpalić. Są jeszcze takie zakłady, gdzie nie buduje się więcej jak kilka nowych form rocznie. Tam tradycyjne podejście może być wystarczające, ale są też wspomniane „fabryki form”, gdzie ciągle goni się za wyższą wydajnością i nie ma nigdy „wystarczających” rozwiązań.
„Nieaktualny schemat” jest dość dobrze znany i można go znaleźć w wielu źródłach, być może z tej przyczyny, że jeden „aktualny schemat” w zasadzie nie istnieje, ponieważ jest on przez cały czas aktualizowany. Ponadto aktualizacja ta przebiega różnie w zależności od branży, a nawet pojedynczej firmy. Dobrym przykładem jest przemysł samochodowy, ponieważ innymi „schematami” posługuje się np. przemysł niemiecki, a innymi przemysł amerykański. Na wysokim poziomie uogólnienia można jednak pewne wspólne elementy wyróżnić.
1. Analiza techniczno-ekonomiczna
Na tym, pierwszym etapie analizie podlegają wejściowe założenia projektowe, czyli w głównej mierze dokumentacja wypraski, a w szczególności model 3D. Dwuwymiarowe rysunki jeśli są używane, to stanowią już raczej tylko funkcję pomocniczą.
Pod pojęciem analiza techniczna kryje się tutaj analiza technologiczności konstrukcji wypraski. Sprawdza się założone kierunki rozformowania i odpowiadające im pochylenia i grubości ścian, ale przede wszystkim wykonuje się symulację wtryskiwania. W branży bardzo często ten cały szereg analiz określa się jako „DfM”, co nie jest do końca poprawne, gdyż znaczenie pojęcia Projektowania zorientowanego na wytwarzanie (ang. Design for Manufacturing) jest znacznie szersze niż sama tylko analiza technologiczności projektu detalu (więcej o tym można znaleźć tutaj).
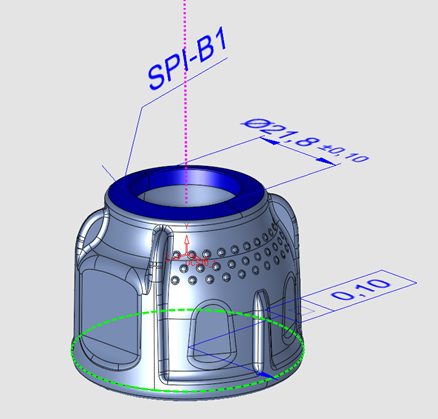
Rysunek 2 Przykład modelu 3D wypraski z naniesionymi tolerancjami wymiarowymi i chropowatością powierzchni
W szczegółach „DfM” jest różny w różnych firmach, ale zawsze jego wynikiem powinno być jasne określenie, czy ofertowany detal jest wykonywalny z zachowaniem wymogów klienta. Jeżeli już na tym etapie wyniki symulacji pokazują np. znaczne deformacje i przekroczenie wymaganych tolerancji wymiarowych, to nie ma co się łudzić, że na kolejnych etapach projektu „jakoś wyjdziemy na prostą”. Największą bolączką tego etapu projektu jest lekceważenie, lub błędna interpretacja wyników analiz symulacyjnych.
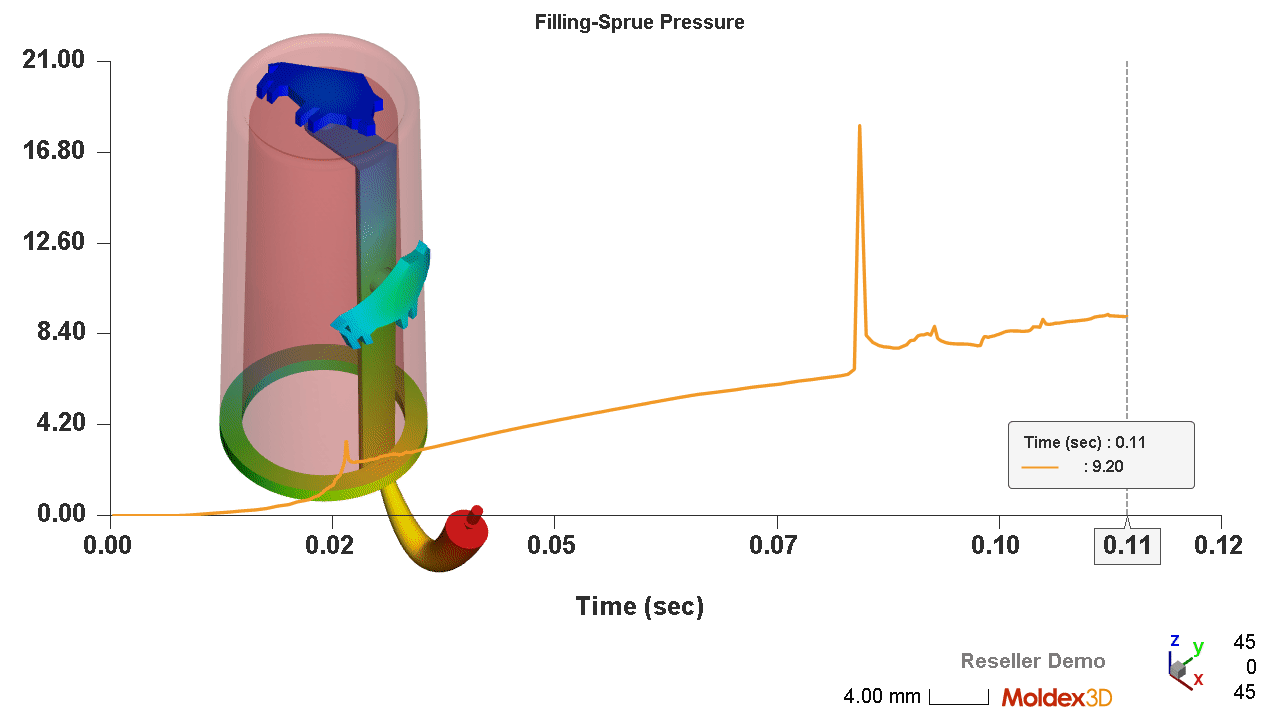
Rysunek 3 Przykładowy wynik wstępnej symulacji wtrysku Moldex3D
Równolegle do analiz technicznych prowadzone są analizy ekonomiczne (stąd nazwa „Analiza techniczno-ekonomiczna”). Tutaj na podstawie wielkości i czasu realizacji zamówienia określa się wymaganą krotność formy, oczekiwany czas jej pracy (tzw. „trwałość”) i czas cyklu wtryskiwania. W tym miejscu łączą się aspekty ekonomiczne i techniczne, gdyż opłacalny czas cyklu może nie zgadzać się z tym techniczne możliwym, wyliczonym podczas symulacji.
Końcowym wynikiem analizy techniczno-ekonomicznej zawsze powinien być jasny wniosek czy dana wypraska jest możliwa do wytworzenia i czy to wytwarzanie jest opłacalne. W przypadku gdy tego wniosku nie da się postawić, może zapaść decyzja o budowie formy prototypowej i potrzebie doświadczalnej weryfikacji możliwości spełnienia wymagań zleceniodawcy.
2. Analiza koncepcyjna
Jeśli z pierwszego etapu wynika, że jesteśmy w stanie wytworzyć wypraskę zgodnie z wymaganiami klienta, w zadanych przez niego czasie i cenie to kolejnym krokiem jest analiza koncepcyjna budowy formy. Tutaj określa się:
- Sposób doprowadzenia tworzywa (przebieg kanałów wlewowych),
- Sposób odbioru ciepła (przebieg kanałów chłodzących),
- Sposób usuwania wypraski i wlewka (miejsca wypychaczy, miejsca suwaków, wypychaczy skośnych, rdzeni itd.).
Do każdego z ww. punktów stosuje się symulacje numeryczne. Ewentualne odkształcenia powstałe podczas rozformowywania i wypychania wypraski również można przewidzieć.
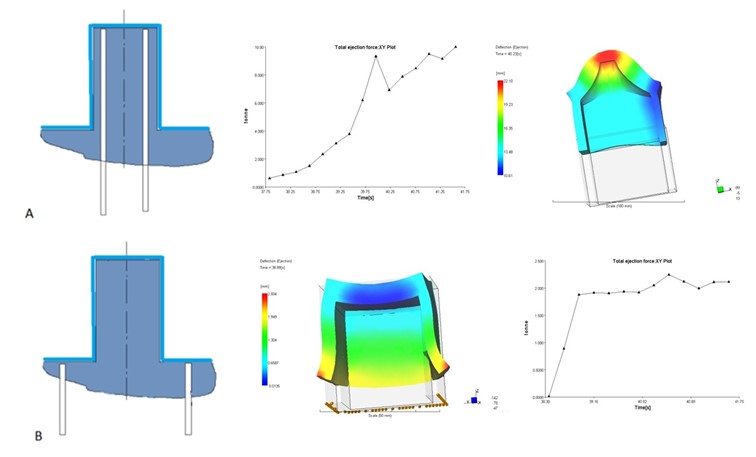
Rysunek 4 Obliczenia przebiegu siły wypychania i odkształceń wypraski [2]
Warto nadmienić, że zarówno umiejscowienie przewężek jak i przebieg linii podziału jest na tym etapie wartością wejściową. Zazwyczaj zostaje to już określone przez klienta i ewentualnie jest to „dookreślane” na etapie analizy techniczno-ekonomicznej. Teraz należy zdefiniować sposób technicznej realizacji powyższych założeń.
Wynikiem tego etapu jest szkic koncepcyjny formy, czyli model zawierający: schemat układu chłodzenia, rozmieszczenie gniazd, wymiary gabarytowe formy (tzw. „skrzynkę”), schemat układu wlewowego, wskazane pole wypychania na wyprasce, określone przestrzenie robocze elementów ruchomych (suwaki, rdzenie itd.). Oprócz tego bardzo często sporządza się osobny dokument tzw. Specyfikację warunków technicznych formy wtryskowej. Dokument ten jest szczególnie przydatny, a w zasadzie niezbędny gdy wykonanie formy zleca się zewnętrznej narzędziowni. W skład tego dokumentu zazwyczaj wchodzą:
- Model wypraski wraz z opisem (w szczególności należy podać dokładną nazwę tworzywa, a nawet załączyć kartę materiałową; wymogi kształtowo-wymiarowe, chropowatości powierzchni, oznaczenia powierzchni pierwszoplanowych i funkcyjnych, wartość skurczu poprzecznego i wzdłużnego wyliczonego z symulacji, szacowaną masę wypraski),
- Dane techniczne wtryskarki (m.in. wymiary przestrzeni montażowej formy, charakterystykę układu uplastyczniającego),
- Typ pracy formy (automatyczny, półautomatyczny, współpraca z robotem, pickerem itd.),
- Wymagana trwałość formy mierzona ilością cykli,
- Opis budowy formy:
- Rodzaj zabudowy gniazda w płycie (gniazdo we wstawkach, modułowe itp.),
- Typ układu wlewowego (zimny, gorący kanał i sprecyzowanie ewentualnego dostawcy GK),
- Typ napędu układu wypychania i elementów formujących (wyrzutnik dwutaktowy, dodatkowe siłowniki hydrauliczne, elektryczne, krzywki itd.),
- Prowadzenie i ustalenie połówek formy,
- Opis układu termoregulującego (typ chłodziwa, podłączenia, dozwolona minimalna średnica kanału, zakres temperatury pracy itd.),
- Wymagane opisy i oznaczenia (tablice znamionowe, grawerunki),
- Nazwa dostawcy normaliów,
- Wyniki symulacji i obliczeń szkicu koncepcyjnego wraz z wnioskami,
- Opis warunków akceptacji konstrukcji formy.
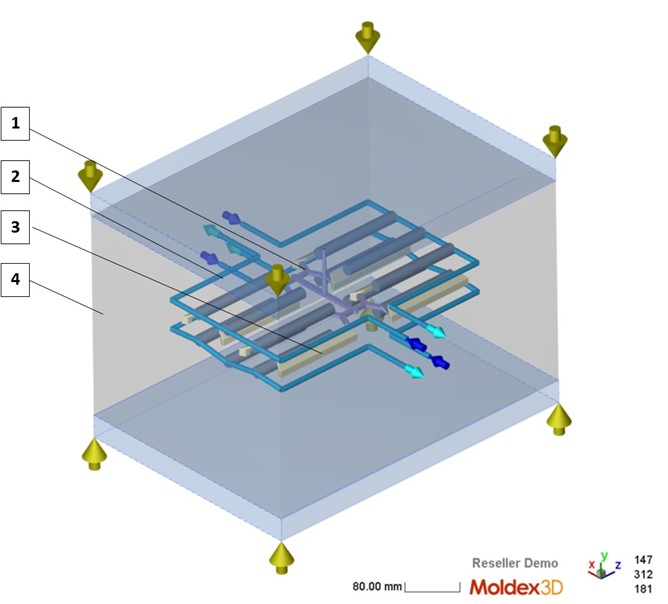
Rysunek 5 Możliwy wygląd szkicu koncepcyjnego formy; 1 – układ wlewowy, 2 – układ chłodzenia, 3 – wypraska, 4 – gabaryt formy
Częstą praktyką jest zawarcie informacji ze specyfikacji formy w modelu szkicu koncepcyjnego i dodatkowo dołączanie zakładowego standardu budowy form. Tym sposobem ogólne wiadomości na temat dozwolonych praktyk stosowanych w przedsiębiorstwie są treścią tylko jednego dokumentu, a dane specyficzne dla danego projektu znajdują się bezpośrednio w tym projekcie.
3. Konstrukcja form wtryskowych
No i w końcu można się zabrać do roboty. Dopiero po sprawdzeniu czy się da, czy się opłaca i czy wiemy jak to zrobić, możemy „postawić pierwszą kreskę” w programie CAD. „Pierwsza kreska” w tym przypadku to zaimportowanie modelu wypraski i przeskalowanie go zgodnie ze współczynnikami skurczu. Kolejnym krokiem jest zamodelowania powierzchni podziałowych i zabudowa gniazda.
Rysunek 6 Wyznaczenie powierzchni podziałowych w programie Cimatron
Kolejnymi etapami zazwyczaj są: wrysowanie segmentów formujących (suwaków, rdzeni), wrysowanie układu wlewowego, wrysowanie układu wypychania wypraski i wlewka, wrysowanie kanałów regulacji temperatury, konstrukcja napędów płyt, wypychaczy segmentów, oraz dobór i wrysowanie elementów ustalająco-prowadzących. Nie jest to oczywiście jedyna możliwa i słuszna procedura, ale zwykle konstruktor „rozprzestrzenia” zasięg swoich prac zaczynając od gniazda i podziału formy, a na układzie wypychania wypraski kończąc.
Efektem tego etapu projektowania formy jest tzw. „osiemdziesiątka” (nazwa wzięta od zakładanego 80% postępu nad modelem formy) lub „szkic koncepcyjny drugi”. W obu przypadkach chodzi oczywiście o jedno i to samo czyli projekt 3D formy zawierający już właściwie wszystkie najistotniejsze elementy. Jedynym czego zwykle jeszcze brakuje to elementy złączne i pomocnicze (krućce, czujniki krańcowe, elementy transportowe, śruby itd.).
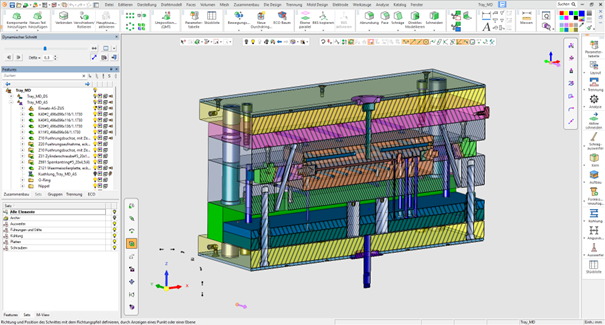
Rysunek 7 „Model formy 80% ” w programie Cimatron
Projekt w tym stanie podlega weryfikacji – sprawdzeniu zgodności konstrukcji ze specyfikacją wynikającą z analizy koncepcyjnej i walidacji, która polega w głównej mierze na symulacji wtrysku uwzględniającej kluczowe układy formy i interpretacji otrzymanych wyników. Bardzo często też dochodzi do korekty wymiarowej gniazda i współczynników skurczu wypraski na podstawie danych z symulacji uwzględniających cały projekt formy. Negatywna walidacja bądź weryfikacja wymusza oczywiście zmiany w konstrukcji. Pozytywne wyniki natomiast kierują nas już prosto w stronę finału, którym jest:
4. Rysunek złożeniowy
Ów rysunek już praktycznie prawie zawsze rysunkiem nie jest. Jest to model 3D złożenia formy ze wszystkimi częściami, których może być kilkaset. Lista tych części jest osobnym plikiem (nie jak kiedyś tabelą na rysunku), lub po prostu rekordem w bazie. Projekty form wtryskowych jak każdych innych produktów zapisuje się w relacyjnych systemach typu PLM, gdzie do pliku z modelem 3D można przypisać BOM (listę części), raport z odbioru formy itd.
Po zatwierdzeniu ostatecznej wersji projektu rysunek złożeniowy „idzie na warsztat”, gdzie projektowana jest obróbka części nieznormalizowanych w systemie CAM. Modele tych części muszą być odpowiednio „pokolorowane”, aby program był w stanie odczytać tolerancje przypisane odpowiednim powierzchniom. Dziś na szczęście komputery częściej „czytają rysunek” niż ludzie i żmudne detalowanie każdej części składowej formy nie jest już konieczne. Co więcej po odpowiednim skonfigurowaniu kodowania barwą w dedykowanym do projektowania form środowisku CAD, kolory są automatycznie przypisywane poszczególnym operacjom. Program „wie” jaki kolor powinny mieć powierzchnie będące wynikiem przycięcia wkładki płaszczyzną podziału, a jaki powierzchnie pogłębienia pod łeb śruby. Oczywiście takie automatyczne „kolorowanie” trzeba jeszcze przed zwolnieniem na warsztat sprawdzić.
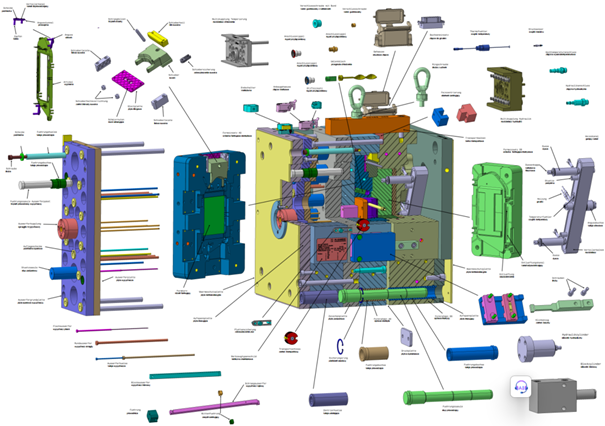
Rysunek 8 Złożoność rysunku złożeniowego

Rysunek 9 Przykład modelu z kodowaniem barwą RGB [3]
Podsumowanie
- Proces projektowania form wraz z postępem informatyki przemysłowej nieustannie się rozwija.
- Rozwój ten jest inny w różnych częściach świata, a nawet w różnych firmach w tym samym mieście. Trudno o jeden powszechnie stosowany standard tego procesu.
- Na wysokim poziomie uogólnienia można mówić o etapach takich jak:
- Studium wykonalności formy (aspekt techniczny i ekonomiczny),
- Opracowanie koncepcji budowy formy,
- Konstrukcja formy,
- Opracowanie dokumentacji wykonawczej.
- Projekt formy wtryskowej jest wynikiem sprzężenia przynajmniej kilku środowisk komputerowych (CAD, CAE, CAM) i umiejętności ludzkich. Nie jest zatem zadaniem trywialnym. Dlatego też coraz częściej jest zlecany przez wtryskownie do specjalizujących się w tym ośrodków zewnętrznych.
Szukając wykonawcy dla Twoich produktów, z wykorzystaniem form wtryskowych, nie musisz posiadać gotowego projektu. Wystarczy pomysł a w reszcie będziemy w stanie Cię wspomóc i poprowadzić od uszczegółowienia pomysłu, poprzez projekt, tworzenie formy aż po wytworzenie gotowego produktu: https://canexpol.pl/nowe-projekty/
Zapraszamy do kontaktu:
email.: projekty@canexpol.pl
tel.: +48 517 889 139
Produkcja Twojego pomysłu pod okiem ekspertów.
Autor: dr inż. Przemysław Narowski – Politechnika Warszawska
Bibliografia
- Pye R. C. W., Injection Mould Design, George Godwin Ltd., 1978
- Bakharev A., Astbury D., AIP Conference Proceedings, Volume 1532, Issue 1
- https://vdwf.de
- Wilczyński K.(red.), Wybrane zagadnienia przetwórstwa tworzyw sztucznych, OWPW, 2011
- https://cimatron.com
- https://moldex3d.com