Metoda wtryskiwania tworzyw sztucznych to jedna z najczęściej stosowanych technologii produkcji, która pozwala na wytwarzanie precyzyjnych i trwałych elementów z tworzyw sztucznych. Aby jednak produkty wtryskowe spełniały wysokie wymagania jakościowe, konieczne jest uwzględnienie wielu kluczowych czynników. W artykule przedstawiono najważniejsze aspekty wpływające na jakość wtryskiwania oraz wskazano, jak zapewnić optymalne rezultaty.
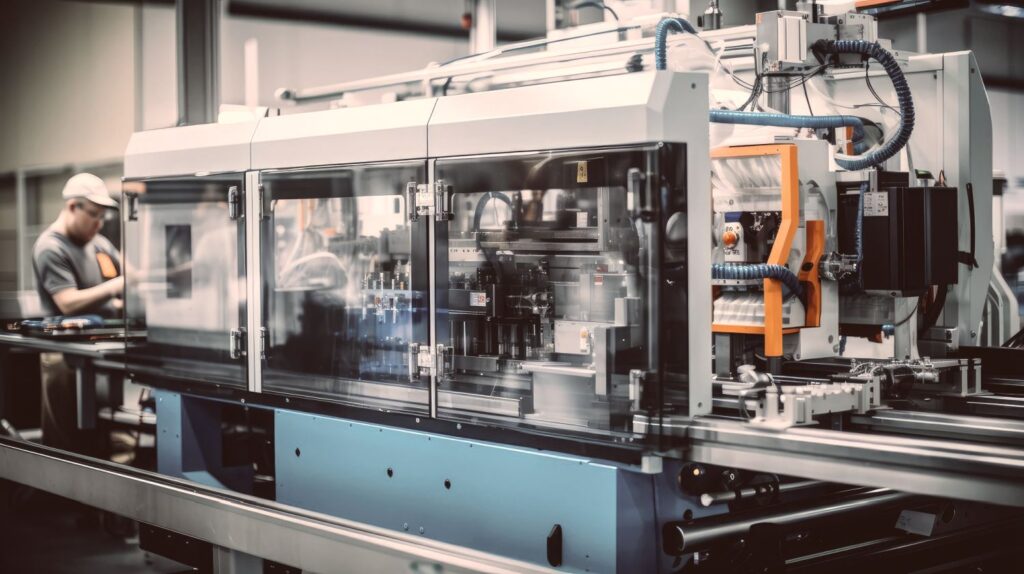
Parametry procesu wtryskiwania
Każdy parametr procesu wtryskiwania wpływa na jakość gotowego wyrobu, dlatego ich precyzyjne dobranie i kontrola mają kluczowe znaczenie. Oto dodatkowe czynniki, które warto wziąć pod uwagę:
1. Szybkość wtrysku
Szybkość, z jaką tworzywo sztuczne jest wprowadzane do formy, wpływa na jakość wypełnienia i równomierne rozprowadzenie materiału. Zbyt wysoka szybkość może powodować powstawanie linii łączenia oraz defektów powierzchniowych, natomiast zbyt niska – niedoformowanie wyrobu.
2. Ciśnienie docisku
Po wypełnieniu formy materiał jest dodatkowo dociskany w celu wyeliminowania pustych przestrzeni i zapobiegania skurczom podczas chłodzenia. Odpowiednie ustawienie ciśnienia docisku pozwala na uzyskanie wymiarowej stabilności produktu.
3. Temperatura formy
Oprócz temperatury samego tworzywa sztucznego, równie ważna jest temperatura formy wtryskowej. Zbyt zimna forma może prowadzić do przedwczesnego stwardnienia tworzywa, co utrudnia dokładne odwzorowanie detali. Z kolei nadmierne nagrzanie formy wydłuża czas chłodzenia i może powodować odkształcenia.
4. Prędkość chłodzenia
Chłodzenie to jeden z najważniejszych etapów cyklu wtryskiwania. Odpowiednie rozplanowanie kanałów chłodzących w formie oraz kontrola prędkości odbierania ciepła zapobiegają powstawaniu naprężeń wewnętrznych i deformacjom.
5. Czas utrzymania ciśnienia
Po wypełnieniu formy przez tworzywo ciśnienie jest utrzymywane przez określony czas, aby kompensować skurcz tworzywa podczas krzepnięcia. Czas ten musi być dostosowany do właściwości materiału i geometrii formy – zbyt krótki może prowadzić do powstawania pustek, a zbyt długi zwiększać czas cyklu i koszty produkcji.
6. Wilgotność tworzywa
Przed wtryskiem materiał powinien być dokładnie wysuszony, aby usunąć wilgoć, która może prowadzić do defektów, takich jak pęcherzyki gazu, osłabienie struktury wyrobu czy niejednolity wygląd powierzchni.
7. Zastosowanie odpowiednich korekcji w trakcie procesu
Proces wtryskiwania wymaga ciągłego monitorowania i wprowadzania korekt, np. w przypadku zmiany warunków otoczenia, takich jak temperatura czy wilgotność powietrza, które mogą wpływać na właściwości materiału.
8. Powtarzalność parametrów
Jednym z kluczowych czynników zapewniających jakość produktów wtryskowych jest stabilność parametrów procesu. Nawet niewielkie odchylenia mogą skutkować powstawaniem wad. Dlatego nowoczesne wtryskiwarki wyposażone są w systemy automatycznej korekty i rejestracji parametrów, które minimalizują ryzyko błędów.
Poprawne ustawienie tych wszystkich parametrów wymaga zaawansowanej wiedzy technologicznej, doświadczenia oraz odpowiedniego sprzętu. Właśnie dlatego wybór zaufanego partnera, takiego jak Canexpol, gwarantuje, że każdy etap procesu wtryskiwania będzie realizowany na najwyższym poziomie.
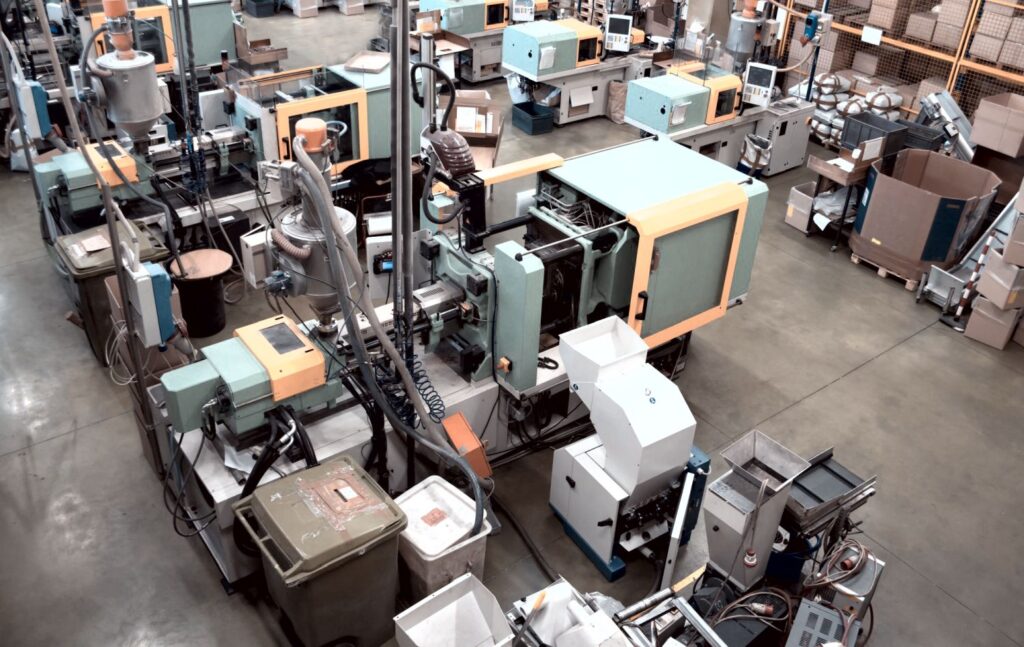
Jakość materiałów do wtryskiwania
Dobór odpowiednich materiałów to jeden z najważniejszych elementów, który decyduje o jakości produktów wtryskowych. Oprócz podstawowych właściwości tworzywa sztucznego, takich jak wytrzymałość czy odporność termiczna, warto zwrócić uwagę na kilka dodatkowych czynników:
1. Modyfikacje tworzyw sztucznych
W zależności od przeznaczenia produktu, surowce mogą być modyfikowane różnymi dodatkami:
- Wypełniacze (np. włókna szklane, talk) – zwiększają wytrzymałość mechaniczną i odporność na odkształcenia.
- Stabilizatory UV – poprawiają odporność na działanie promieniowania słonecznego, co jest kluczowe dla produktów przeznaczonych do użytku zewnętrznego.
- Barwniki i pigmenty – pozwalają na uzyskanie pożądanej estetyki wyrobu, bez kompromisów w jego właściwościach technicznych.
- Plastyfikatory – stosowane w materiałach wymagających większej elastyczności, takich jak PVC.
Odpowiednio dobrane dodatki pozwalają na dostosowanie właściwości materiału do wymagań projektu.
2. Standaryzacja i certyfikaty jakości
Materiały do wtryskiwania powinny spełniać określone normy i posiadać odpowiednie certyfikaty, takie jak:
- ISO – gwarantujące wysoką jakość i powtarzalność materiału.
- REACH i RoHS – potwierdzające, że materiał jest bezpieczny dla użytkowników i środowiska.
- FDA – dla tworzyw stosowanych w branży spożywczej lub medycznej.
Stosowanie certyfikowanych tworzyw to nie tylko kwestia jakości, ale również zgodności z regulacjami prawnymi.
3. Recyklaty i materiały zrównoważone
Coraz większą popularność zyskują recyklaty, czyli tworzywa pochodzące z przetworzonych odpadów plastikowych. Ich zastosowanie pozwala na obniżenie kosztów produkcji oraz minimalizację wpływu na środowisko. Ważne jednak, aby jakość recyklatu była odpowiednio kontrolowana, ponieważ zanieczyszczenia mogą negatywnie wpłynąć na trwałość i wygląd produktu końcowego.
Dodatkowo, firmy coraz częściej sięgają po biotworzywa, które są produkowane z surowców odnawialnych (np. PLA) i nadają się do biodegradacji.
4. Przygotowanie materiału przed wtryskiem
Nawet najlepszej jakości tworzywa sztuczne wymagają odpowiedniego przygotowania przed procesem wtryskiwania:
- Suszenie tworzywa – kluczowe, aby usunąć wilgoć, która może prowadzić do defektów, takich jak porowatość czy osłabienie struktury wyrobu. Czas i temperatura suszenia zależą od rodzaju materiału (np. poliamidy są szczególnie podatne na pochłanianie wilgoci).
- Homogenizacja granulatu – równomierne wymieszanie materiału zapewnia spójne właściwości mechaniczne i kolorystyczne gotowego produktu.
5. Wybór materiału w zależności od zastosowania
Każdy produkt wymaga dostosowania tworzywa do jego funkcji i warunków użytkowania. Przykłady:
- Produkty narażone na wysokie temperatury (np. części samochodowe) wymagają materiałów odpornych na działanie ciepła, takich jak PEEK czy PPS.
- Elementy mające kontakt z żywnością muszą być wykonane z tworzyw bezpiecznych, jak polipropylen (PP) lub polietylen (PE).
- Wyroby wymagające estetycznego wykończenia powierzchni (np. obudowy sprzętu elektronicznego) powinny być produkowane z materiałów o wysokiej płynności, które dobrze wypełniają detale formy.
6. Znaczenie współpracy z dostawcami
Współpraca z zaufanymi dostawcami surowców pozwala na zapewnienie ciągłości dostaw materiałów o wysokiej i powtarzalnej jakości. Dostawcy często oferują wsparcie techniczne, pomagając w doborze odpowiedniego tworzywa do konkretnych zastosowań.
W firmie Canexpol szczególną wagę przywiązuje się do jakości stosowanych materiałów. Nasz zespół dokładnie analizuje potrzeby klienta, dobiera najlepsze surowce oraz dba o ich właściwe przygotowanie, co gwarantuje powstanie produktów o doskonałych właściwościach i estetyce.
Znaczenie form wtryskowych
Formy wtryskowe to serce procesu wtryskiwania, od którego zależy nie tylko jakość produktów, ale także efektywność i opłacalność całej produkcji. Warto zwrócić uwagę na dodatkowe aspekty związane z projektowaniem, budową i eksploatacją form wtryskowych.
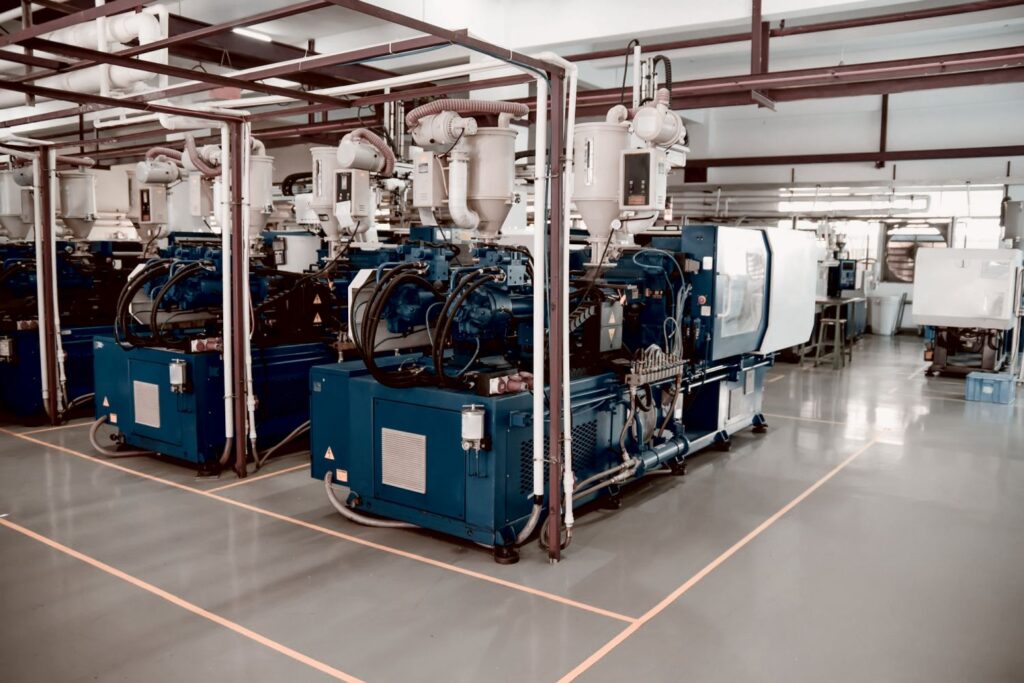
1. Precyzyjne projektowanie form wtryskowych
Projekt formy powinien uwzględniać wszystkie szczegóły techniczne i wymogi produktu. Kluczowe znaczenie mają:
- Konstrukcja gniazd formujących – każde gniazdo odpowiada za odwzorowanie kształtu produktu. Nawet najmniejsze niedokładności w projekcie mogą prowadzić do defektów, takich jak nierówności czy niedokładne wymiarowanie.
- System wlewków i kanałów doprowadzających – dobrze zaprojektowany system doprowadza tworzywo równomiernie do wszystkich gniazd, zapobiegając powstawaniu naprężeń i wad.
- Uwzględnienie skurczu tworzywa – różne materiały wtryskowe kurczą się w różnym stopniu podczas chłodzenia, co należy uwzględnić w projekcie formy.
2. Materiał użyty do budowy formy
Wybór odpowiedniego materiału na formę wtryskową wpływa na jej trwałość oraz jakość produktów. Najczęściej stosowane są:
- Stale narzędziowe – idealne do produkcji masowej ze względu na wysoką odporność na ścieranie i długą żywotność.
- Aluminium – lekkie i tańsze, wykorzystywane głównie do krótkich serii lub prototypów.
- Materiały z powłokami antykorozyjnymi – szczególnie ważne w przypadku pracy z tworzywami zawierającymi dodatki ścierne lub w wilgotnym środowisku.
Warto zainwestować w materiały wysokiej jakości, które minimalizują ryzyko uszkodzeń i zmniejszają koszty konserwacji.
3. System chłodzenia w formach wtryskowych
Efektywny system chłodzenia ma kluczowe znaczenie dla jakości i czasu produkcji. Należy zwrócić uwagę na:
- Rozmieszczenie kanałów chłodzących – ich optymalne ułożenie zapewnia równomierne odbieranie ciepła, co zapobiega odkształceniom produktu.
- Rodzaj medium chłodzącego – najczęściej stosowana jest woda, jednak w niektórych przypadkach wykorzystuje się płyny o lepszej przewodności cieplnej, np. glikole.
- Sterowanie temperaturą – zaawansowane formy pozwalają na precyzyjne kontrolowanie temperatury w różnych sekcjach, co jest szczególnie ważne przy produkcji skomplikowanych wyrobów.
4. Liczba gniazd w formie
Formy mogą być jedno- lub wielogniazdowe, a wybór odpowiedniej zależy od skali produkcji i złożoności wyrobu:
- Formy jednogniazdowe – stosowane do małych serii lub produktów o wysokich wymaganiach jakościowych.
- Formy wielogniazdowe – zwiększają wydajność produkcji, umożliwiając jednoczesne wytwarzanie wielu produktów. Ważne jest jednak, aby zapewnić równomierne wypełnienie wszystkich gniazd, co wymaga precyzyjnego projektu.
5. Automatyzacja w formach wtryskowych
Nowoczesne formy często wyposażone są w dodatkowe elementy automatyzujące proces:
- Mechanizmy wypychające – zapewniają szybkie i bezpieczne usuwanie gotowego wyrobu z formy, co skraca czas cyklu.
- Rdzenie obrotowe i suwaki – umożliwiają produkcję bardziej skomplikowanych kształtów, takich jak gwinty czy podcięcia.
- Czujniki i systemy monitorowania – pozwalają na bieżąco kontrolować parametry procesu, takie jak ciśnienie, temperatura czy czas cyklu, co zwiększa powtarzalność produkcji.
6. Konserwacja i regeneracja form wtryskowych
Formy wtryskowe są narażone na intensywne użytkowanie, dlatego ich regularna konserwacja jest kluczowa:
- Czyszczenie formy – usuwa resztki tworzywa i zanieczyszczenia, które mogą wpływać na jakość wyrobów.
- Smarowanie elementów ruchomych – minimalizuje zużycie mechanizmów i zapewnia płynność pracy.
- Regeneracja formy – w przypadku zużycia lub uszkodzeń możliwa jest wymiana zużytych elementów, co wydłuża żywotność formy i obniża koszty produkcji w dłuższym okresie.
7. Współpraca z ekspertami w zakresie form wtryskowych
Tworzenie form wtryskowych to skomplikowany proces, który wymaga doświadczenia oraz specjalistycznej wiedzy. Dlatego współpraca z zaufanym partnerem, takim jak firma Canexpol, gwarantuje:
- Projektowanie form dostosowanych do indywidualnych potrzeb klienta.
- Stosowanie wysokiej jakości materiałów i technologii.
- Kompleksową obsługę, w tym serwis i konserwację form.
Dobrze zaprojektowana i utrzymana forma wtryskowa to inwestycja, która przekłada się na wyższą jakość produktów, mniejsze ryzyko przestojów i większą efektywność produkcji. W firmie Canexpol przykładamy ogromną wagę do tego, aby każda forma była precyzyjnie wykonana i dostosowana do potrzeb klienta, gwarantując tym samym niezawodność i perfekcyjne rezultaty.
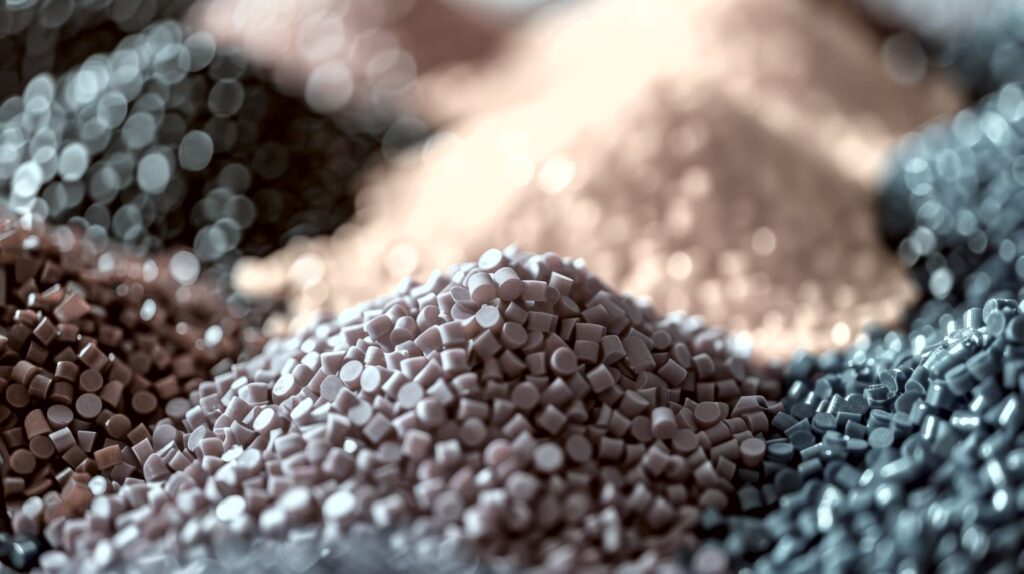
Wtryskiwarki i ich wpływ na jakość wtryskiwania
Nowoczesne wtryskiwarki odgrywają kluczową rolę w procesie wtryskiwania tworzyw sztucznych. Ich jakość, precyzja i zaawansowanie technologiczne bezpośrednio przekładają się na efektywność produkcji, powtarzalność oraz jakość gotowych produktów wtryskowych. Oto dodatkowe aspekty, które warto uwzględnić przy analizie znaczenia wtryskarek:
1. Precyzja działania wtryskarki
Wysokiej klasy wtryskiwarki umożliwiają dokładną kontrolę parametrów procesu, takich jak:
- Ciśnienie wtryskiwania – zapewnia odpowiednie rozprowadzenie tworzywa w formie, eliminując ryzyko powstawania pustek lub niedolania materiału.
- Prędkość wtrysku – wpływa na jakość wypełnienia detali, zwłaszcza w przypadku skomplikowanych form.
- Temperatura materiału i formy – precyzyjne utrzymanie temperatur minimalizuje ryzyko przegrzania lub niedogrzania tworzywa, co mogłoby prowadzić do wad strukturalnych.
Zaawansowane systemy sterowania pozwalają na monitorowanie tych parametrów w czasie rzeczywistym, co zwiększa powtarzalność produkcji.
2. Rodzaje wtryskarek
Wybór odpowiedniego typu wtryskarki jest istotny, ponieważ różne modele oferują odmienne właściwości:
- Wtryskarki hydrauliczne – sprawdzają się w produkcji dużych elementów, ponieważ zapewniają dużą siłę zamykania i są bardziej odporne na obciążenia mechaniczne.
- Wtryskarki elektryczne – oferują wyjątkową precyzję i szybkość działania, dzięki czemu idealnie nadają się do produkcji detali o wysokich wymaganiach jakościowych. Dodatkowo są energooszczędne i bardziej ekologiczne.
- Wtryskarki hybrydowe – łączą zalety obu typów, oferując jednocześnie dużą siłę i precyzję.
Dobór odpowiedniego rodzaju wtryskarki zależy od specyfiki projektu, rozmiaru produktu oraz wymagań dotyczących wydajności.
3. Znaczenie siły zamykania
Siła zamykania wtryskarki musi być dostosowana do wielkości formy oraz ciśnienia wtryskiwania. Zbyt niska siła zamykania może prowadzić do wypływów materiału (tzw. „flash”), natomiast nadmierna siła może powodować uszkodzenia formy. Precyzyjne dobranie tego parametru jest kluczowe dla jakości i ekonomiki procesu.
4. Automatyzacja i cyfryzacja wtryskarek
Nowoczesne wtryskarki są coraz częściej wyposażone w systemy automatyzacji, które poprawiają jakość procesu i zmniejszają ryzyko błędów:
- Czujniki ciśnienia i temperatury – umożliwiają bieżące monitorowanie procesu i szybkie reagowanie na odchylenia od normy.
- Systemy analizy danych – pozwalają na analizę parametrów procesu w czasie rzeczywistym, co ułatwia optymalizację produkcji.
- Integracja z robotami – wtryskarki mogą współpracować z robotami, które automatyzują odbiór produktów, cięcie wlewków lub układanie gotowych elementów, co zwiększa efektywność całego procesu.
Automatyzacja nie tylko poprawia jakość produktów, ale także obniża koszty produkcji, zmniejszając czas cyklu i ryzyko przestojów.
5. Zużycie energii i wpływ na środowisko
Współczesne wtryskarki są projektowane z myślą o energooszczędności. Modele elektryczne i hybrydowe zużywają mniej energii niż tradycyjne maszyny hydrauliczne, co jest korzystne zarówno dla środowiska, jak i kosztów produkcji. Zastosowanie energooszczędnych technologii wpływa na:
- Obniżenie emisji CO₂.
- Ograniczenie strat ciepła.
- Lepsze wykorzystanie surowców dzięki mniejszej ilości odpadów produkcyjnych.
6. Wydajność i powtarzalność
Jedną z najważniejszych zalet nowoczesnych wtryskarek jest ich zdolność do utrzymania wysokiej powtarzalności procesu. Oznacza to, że każdy produkt wytwarzany w danej serii jest identyczny pod względem wymiarów, właściwości i wyglądu. Powtarzalność jest kluczowa w branżach wymagających precyzji, takich jak:
- Motoryzacja (np. produkcja części technicznych).
- Elektronika (np. obudowy urządzeń).
- Medycyna (np. wyroby medyczne i diagnostyczne).
7. Serwis i konserwacja wtryskarek
Długotrwała i efektywna praca wtryskarki zależy od regularnej konserwacji i serwisowania. Zaniedbanie tych działań może prowadzić do:
- Niestabilności procesu wtryskiwania.
- Szybszego zużycia części maszyn, takich jak ślimaki czy cylindry.
- Przestojów produkcyjnych, które generują dodatkowe koszty.
W firmie Canexpol dbamy o to, aby nasze wtryskarki były utrzymywane w doskonałym stanie technicznym, co gwarantuje niezawodność i wysoką jakość produkcji.
Nowoczesne wtryskarki są fundamentem efektywnej i jakościowej produkcji. Inwestowanie w zaawansowany sprzęt oraz jego profesjonalną obsługę to jeden z kluczowych elementów sukcesu w branży wtryskiwania tworzyw sztucznych. Dzięki takiemu podejściu firma Canexpol zapewnia swoim klientom produkty o najwyższych standardach jakości.

Kontrola jakości wtryskiwania
Kontrola jakości wtryskiwania jest kluczowym etapem, który pozwala zapewnić, że gotowe produkty spełniają wymagania techniczne, estetyczne oraz funkcjonalne. Skuteczna kontrola wymaga zastosowania odpowiednich narzędzi, procedur i technologii, które minimalizują ryzyko wystąpienia wad, zwiększają powtarzalność procesu oraz optymalizują koszty produkcji.
1. Etapy kontroli jakości w procesie wtryskiwania
Kontrola jakości powinna być prowadzona na każdym etapie procesu:
- Kontrola wejściowa materiałów – przed rozpoczęciem produkcji weryfikuje się jakość granulatu tworzywa sztucznego, sprawdzając jego wilgotność, czystość oraz zgodność z dokumentacją techniczną.
- Monitorowanie parametrów procesu w czasie rzeczywistym – na etapie produkcji rejestruje się takie parametry, jak ciśnienie wtryskiwania, temperatura tworzywa i formy czy czas cyklu wtryskiwania. Odchylenia od normy mogą wskazywać na potencjalne problemy, które należy natychmiast skorygować.
- Kontrola wyrobów końcowych – gotowe produkty są sprawdzane pod kątem wymiarów, kształtu, powierzchni oraz innych kluczowych cech.
2. Technologie stosowane w kontroli jakości
Nowoczesne metody kontroli jakości wtryskiwania pozwalają na wykrywanie nawet najmniejszych odchyleń:
- Skanery 3D i pomiary optyczne – pozwalają na precyzyjną kontrolę wymiarów oraz geometrii produktów. Porównanie wyników z modelem CAD umożliwia szybkie wykrycie defektów, takich jak deformacje czy niedokładności w detalach.
- Badania nieniszczące (NDT) – np. ultradźwiękowe, które pozwalają na wykrycie wad wewnętrznych, takich jak pęcherze powietrza czy niedolania materiału.
- Mikroskopia i analiza struktury powierzchni – stosowane w przypadku produktów o wysokich wymaganiach estetycznych lub technicznych, takich jak elementy medyczne czy elektroniczne.
3. Częste defekty w procesie wtryskiwania i ich przyczyny
Dzięki regularnej kontroli jakości można wykryć i wyeliminować typowe defekty, takie jak:
- Wypływki – nadmiar materiału na krawędziach produktu, wynikający z niedostatecznej siły zamykania formy.
- Pęcherze powietrza lub porowatość – spowodowane niewłaściwym odgazowaniem lub zbyt szybkim wtryskiem.
- Przegrzanie tworzywa – skutkujące przebarwieniami lub osłabieniem struktury materiału.
- Skurcze i odkształcenia – wynikające z nierównomiernego chłodzenia formy.
- Niedolania – gdy materiał nie wypełnia całkowicie formy, co może być spowodowane zbyt niskim ciśnieniem wtryskiwania lub nieodpowiednią płynnością tworzywa.
Systematyczna analiza przyczyn tych defektów pozwala na ciągłe doskonalenie procesu.
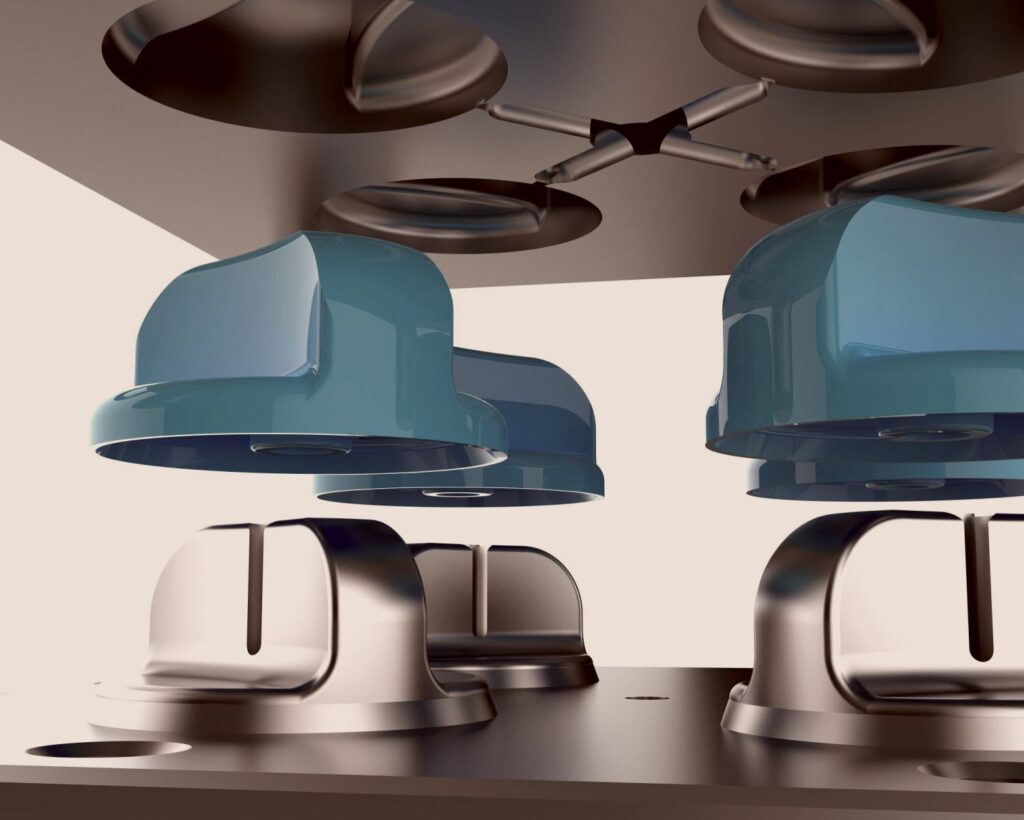
4. Automatyzacja kontroli jakości
W nowoczesnych liniach produkcyjnych coraz częściej stosuje się zautomatyzowane systemy kontroli jakości, które pozwalają na szybsze i bardziej precyzyjne wykrywanie wad. Do najczęściej stosowanych rozwiązań należą:
- Systemy wizyjne – kamery o wysokiej rozdzielczości monitorujące produkty bezpośrednio na linii produkcyjnej, wykrywające wady powierzchniowe, takie jak rysy, pęknięcia czy przebarwienia.
- Roboty inspekcyjne – mogą przeprowadzać szczegółowe pomiary wyrobów oraz eliminować wadliwe elementy bez przerywania procesu produkcji.
- Integracja z IoT (Internet of Things) – dane z wtryskarek i urządzeń kontrolnych są zbierane w czasie rzeczywistym, analizowane i wykorzystywane do optymalizacji procesu.
Automatyzacja kontroli jakości zwiększa wydajność produkcji, redukuje koszty związane z reklamacjami i eliminuje potrzebę ręcznej weryfikacji każdego produktu.
5. Weryfikacja zgodności z normami i certyfikaty jakości
Kontrola jakości wtryskiwania często musi uwzględniać wymagania branżowe oraz regulacje prawne, szczególnie w przypadku produktów dla przemysłu motoryzacyjnego, medycznego czy spożywczego. Do najważniejszych norm należą:
- ISO 9001 – potwierdza, że firma stosuje skuteczny system zarządzania jakością.
- ISO 13485 – dla produktów medycznych.
- FDA oraz HACCP – dla wyrobów mających kontakt z żywnością.
- PPAP (Production Part Approval Process) – wymagany w branży motoryzacyjnej, aby potwierdzić zgodność procesu produkcyjnego z wymaganiami klienta.
Certyfikaty są dowodem na wysoką jakość produktów i procesów, co zwiększa zaufanie klientów.
6. Korzyści z efektywnej kontroli jakości
Skuteczna kontrola jakości to nie tylko eliminacja wad, ale także:
- Zmniejszenie strat materiałowych i kosztów związanych z odpadami.
- Zwiększenie satysfakcji klienta dzięki dostarczaniu produktów zgodnych z wymaganiami.
- Lepsza reputacja firmy na rynku, co przekłada się na większą konkurencyjność.
W firmie Canexpol kontrola jakości wtryskiwania jest priorytetem. Dzięki zaawansowanym technologiom, regularnym audytom i precyzyjnym procedurom, firma dostarcza produkty spełniające najwyższe standardy. To podejście gwarantuje klientom nie tylko wysoką jakość, ale także niezawodność i pewność współpracy.
Dlaczego warto wybrać Canexpol?
Wybór odpowiedniego partnera do produkcji wyrobów wtryskowych ma ogromne znaczenie dla jakości i efektywności procesu produkcji. Canexpol to firma z wieloletnim doświadczeniem w branży, która oferuje kompleksową obsługę, obejmującą projektowanie, produkcję i kontrolę jakości wyrobów wtryskowych. Dzięki nowoczesnemu parkowi maszynowemu i zaawansowanym technologiom, firma zapewnia precyzyjną produkcję detali, spełniających najwyższe wymagania.
Dzięki elastyczności w zakresie realizacji zarówno dużych, jak i małych serii, Canexpol dostosowuje się do specyficznych potrzeb swoich klientów. Szybki czas realizacji zamówień, połączony z dbałością o jakość i terminowość, sprawia, że firma jest godnym zaufania partnerem. W procesie produkcji stosowane są innowacyjne rozwiązania, które pozwalają osiągnąć energooszczędność i minimalizować wpływ na środowisko, co zwiększa konkurencyjność oferty.
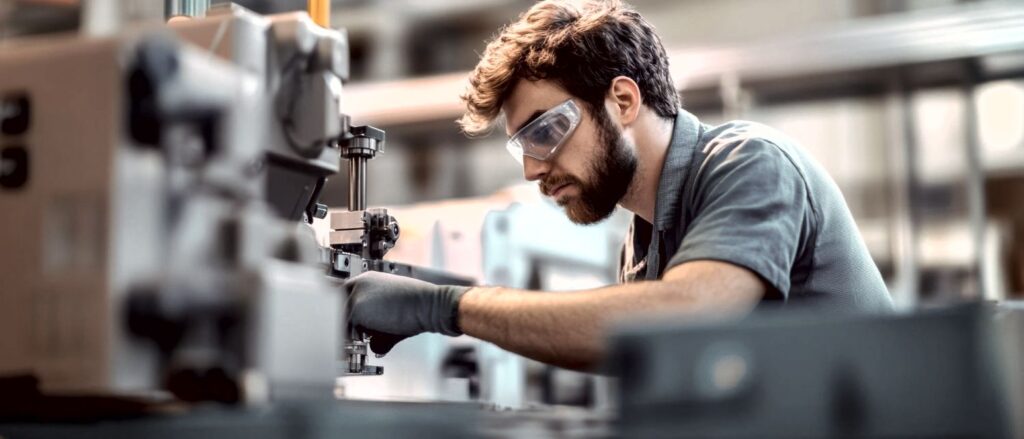
Chciałbyś powierzyć nam swój projekt?
Masz pytania? Wypełnij formularz lub zadzwoń do eksperta:
+48 517 889 139, projekty@canexpol.pl
Canexpol wyróżnia się także profesjonalną obsługą klienta, zapewniając wsparcie na każdym etapie współpracy. Zaufanie, które firma zdobyła wśród swoich partnerów biznesowych, potwierdza jej solidność i niezawodność. Wybierając Canexpol, klienci mogą liczyć na wysoką jakość produktów, terminowość oraz konkurencyjne ceny.