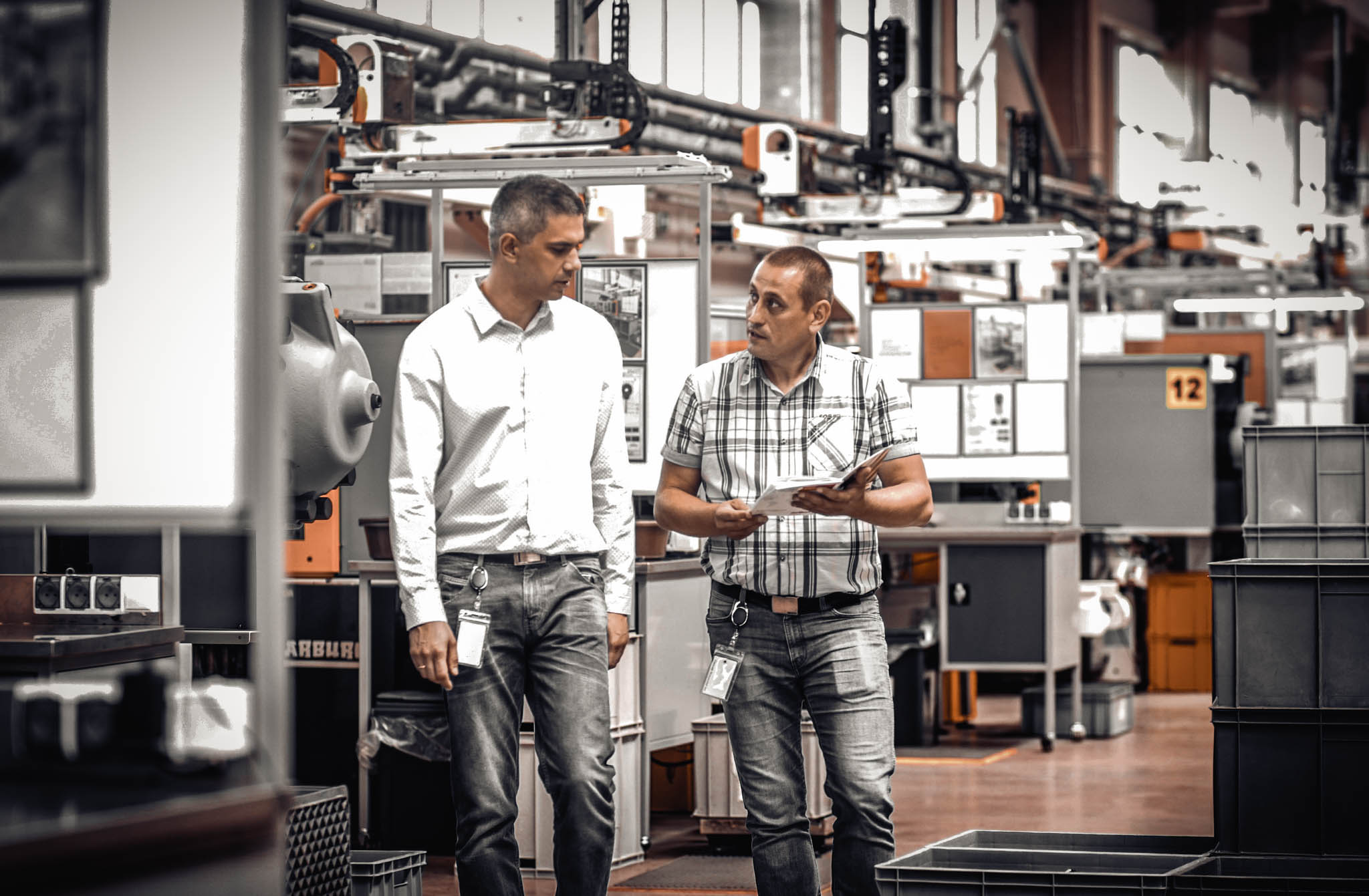
Prosto o niełatwej technologii wtryskiwania
Dzięki swoim unikalnym właściwościom tworzywa sztuczne można przetwarzać różnymi metodami uzyskując przedmioty o bardzo złożonych kształtach ale i cechach fizycznych. Ze względu na specyficzne warunki jakie panują podczas formowania (ciśnienie, szybkość przepływu, prędkość ścinania i inne) każda z metod ma swoje ograniczenia, wady i zalety. Jeśli chodzi o ilość przetwarzanego tworzywa w ujęciu masowym niekwestionowanym liderem jest technologia wytłaczania oraz jej odmiany. To głównie dzięki niej wytwarzane są rury, profile, folie, płyty, opakowania itp. Drugą jest technologia wtryskowego, która pomimo znacznie mniejszego wolumenu charakteryzuje się największą wszechstronnością i zróżnicowaniem produkowanych detali. Zanim przejdziemy do charakterystyki tej pozornie prostej metody przetwórstwa przedstawmy wady i zalety.
Do zalet metody należy zaliczyć:
- Możliwość wytwarzania nawet najbardziej skomplikowanych wyrobów w jednym procesie technologicznym,
- mały bądź żaden udział obróbek wykańczających,
- wysoka jakość i powtarzalność właściwości fizycznych i wymiarów,
- możliwość pełnego zautomatyzowania, komputerowego sterowania i kontroli procesu,
- mniejsze zużycie energii bezpośredniej i wody,
- niewielka pracochłonność,
- niska emisja związków szkodliwych dla otoczenia.
Niestety są i wady:
- Wysoki koszt maszyn (wtryskarek) i niejednokrotnie dorównujący mu koszt oprzyrządowania (form wtryskowych), powodujący wydłużenia czasu amortyzacji i wysokie koszty uruchamiania produkcji (ze względu na to, technologia wtrysku opłacalna tylko przy produkcji wielkoseryjnej i masowej),
- konieczność wysokich kwalifikacji pracowników nadzoru technicznego, którzy muszą znać specyfikę przetwórstwa tworzyw sztucznych, ich przygotowania, ustawiania procesu, pracy z formami wtryskowymi,
- konieczność zachowania wąskich tolerancji parametrów przetwórstwa,
- ograniczona wielkość wytwarzanych elementów wielkością dostępnych maszyn,
- mniejsze zużycie energii bezpośredniej i wody,
- długi czas przygotowania produkcji ze względu na pracochłonność wykonawstwa form wtryskowych,
- konieczność stosowania różnych urządzeń peryferyjnych (podajniki, suszarki, dozowniki, manipulatory, chilery, młynki itp.)
Wtryskiwanie jako proces cykliczny
Zacznijmy od początku. Wtryskiwanie to proces cykliczny polegający na przetłoczeniu uplastycznionego, płynnego tworzywa poprzez kanały doprowadzające formy wtryskowej i przewężki do gniazda formującego nadającego kształt, w którym następuje jego zestalenie podczas ochładzania, a następnie otwarciu formy i wyrzuceniu przez układ wypychania gotowej wypraski lub wyprasek. Wygląda pozornie prosto, ale najważniejsze jest to czego nie widać i czego nie jesteśmy świadomi.Etapy procesu wtryskiwania
Zatem wejdźmy w szczegóły. Wszystko zaczyna się już na etapie przygotowania tworzywa do przetwórstwa. Jedna z nich trzeba suszyć ze względu na ich higroskopijność inne nie ale należy uważać na ich powierzchowne zawilgocenie np. podczas transportu. Jeśli tworzywo wymaga suszenia należy wykorzystać specjalne urządzenia do usunięcia wilgoci. Suszarki mogą mieć różne warunki pracy a tym samym różną wydajność i skuteczność. Ich wielkość za każdym razem należy dobrać do wielkości godzinnej wydajność wtryskarki lub wtryskarek. Kolejny etap to dozowanie do leja zasypowego tworzywa oraz dodatków, których zadaniem jest modyfikacja właściwości fizycznych, zmiana koloru, struktury formowanej wypraski itp. I tu również żeby proces i właściwości wypraski były powtarzalne konieczne jest stosowanie precyzyjnych dozowników. Tak dozowane materiały przedostają się do układu uplastyczniającego, którego zadaniem jest uplastycznianie i transportowanie tworzywa na czoło ślimaka przy jednoczesnym mieszaniu, homogenizacji (ujednorodnianie) zadozowanych materiałów. Uplastycznianie to pierwszy najważniejszy etap kształtujący właściwości reologiczne płynnego tworzywa, które w następnym etapie zostanie wtryśnięte do formy wtryskowej. Niewłaściwie ustawione w tym etapie parametry mogą spowodować degradację tworzywa lub pigmentów, zniszczenie (połamanie) włókna szklanego, wystąpienie niedolewów wypraski itp. Gdy tworzywo jest już przygotowane do wtryśnięcia można rozpocząć kolejny etap – wtryskiwanie, który poprzedza dojazd układu uplastyczniającego do tulei wtryskowej. Po połączeniu układu uplastyczniającego z formą może nastąpić wtrysk, czyli możliwie jak najszybsze przepłynięcie pod wpływem wysokiego ciśnienia (nawet do 2000bar, 200MPa) tworzywa do formy. Przy czym dla uzyskania specyficznych właściwości powierzchni formowanej wypraski lub minimalizowaniu pewnych niedoskonałości (linie łączenia, pułapki powietrzne itp.) należy modyfikować prędkość wtrysku na drodze przepływu w formie. Wymaga to dużego doświadczenia i wnikliwej obserwacji wprowadzanych zmian. Tuż przed całkowitym wypełnieniem formy należy zakończyć fazę wtrysku i łagodnie przejść na fazę docisku. Jest to bardzo newralgiczny etap procesu wypełniania, w którym może wystąpić wiele problemów z tak zwanym przeładowaniem formy ciśnieniem tworzywa i zniszczeniem jej części lub podzespołów. Faza docisku jest odpowiedzialna za uzupełnienie strat w objętości wtryśniętego tworzywa spowodowanego jego skurczem objętościowym, który dla niektórych tworzyw może wynosić nawet powyżej 20%. Dlatego tak ważnym jest zaprojektowanie formy wtryskowej w taki sposób, aby wymiar gniazda formującego był większy o wartość skurczu. Parametry związane z fazą docisku (ciśnienie i czas) są odpowiedzialne również za zminimalizowanie zapadnięć powstałych na powierzchni wypraski. A utrzymywanie go w określonym czasie gwarantuje szybki odpływ ciepła tworzywa do formy wtryskowej, a tym samym wpływa na skrócenie czasu cyklu. Po zakończeniu fazy docisku, która kończy się w momencie zastygnięcia przewężki następuje dalsze jej ochładzanie w fazie chłodzenia. Parametry charakterystyczne dla tej fazy to temperatura formy i czas chłodzenia, kształtują wiele cech wyprasek związanych z ich strukturą co bezpośrednio przekłada się na ich wytrzymałość, dokładność wymiarowo – kształtową, deformacje, sztywność itp. Po zakończeniu tej fazy następuje otwarcie formy wtryskowej i wypchnięcie przez wypychacze wypraski lub odebranie jej za pomocą manipulatora. Ta faza kończy cały cykl formowania.Poszczególne fazy procesu wtryskiwania:
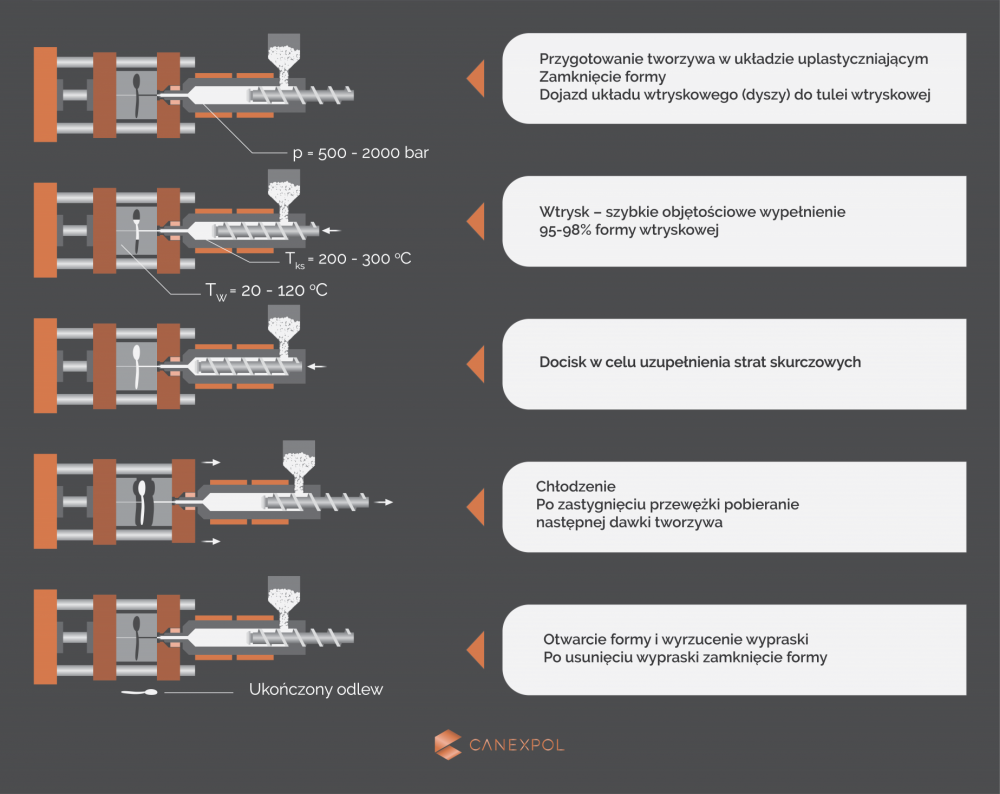
Od czego zależy poprawność formowanych wyprasek?
Należy podkreślić, że proces wtryskiwania kształtuje wiele czynników (nie mylić z parametrami procesu), które mają bezpośredni lub pośredni wpływ na późniejsze cechy fizyczne formowanych wyprasek. Należą do nich: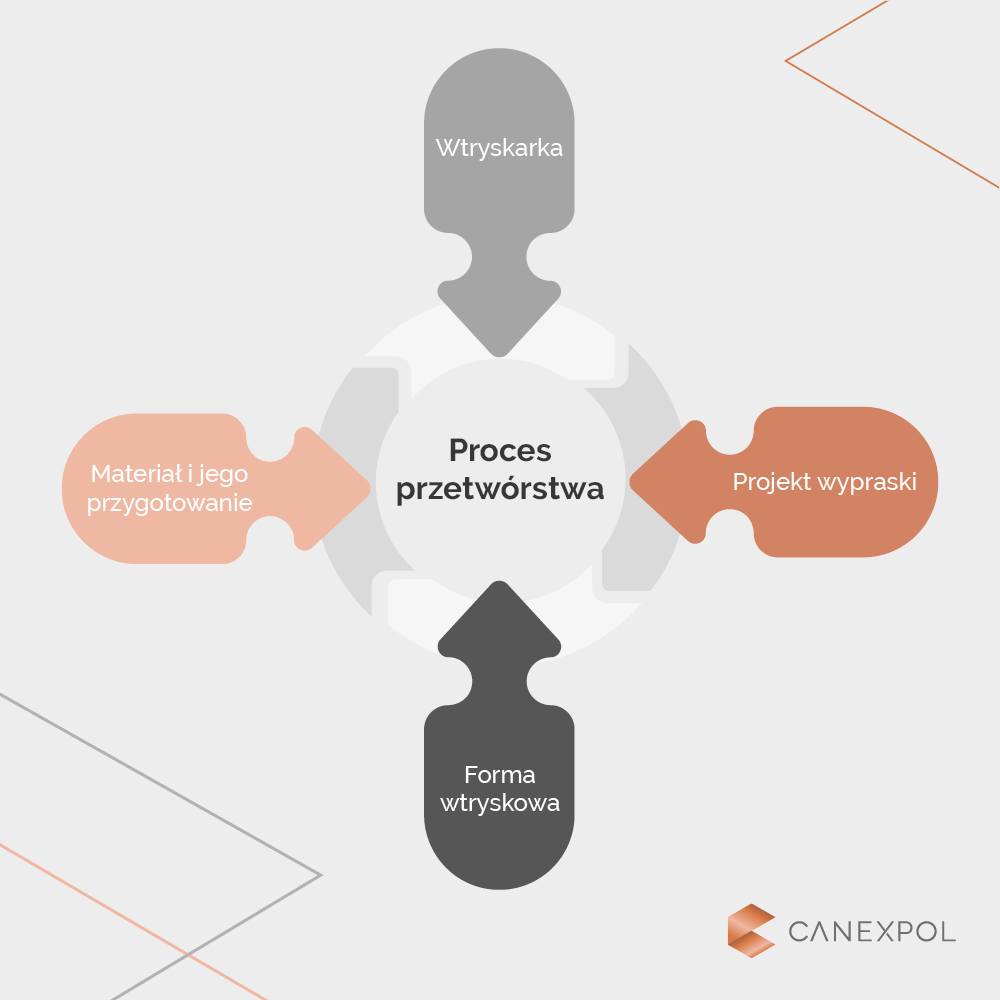
Cenne doświadczenie
Jak widać z pozoru prosty proces ma wiele współzależnych parametrów oraz dużą liczbę czynników, które mogą go zakłócić. Dlatego po wyglądzie wypraski doświadczony operator, ustawiacz jest w stanie wytypować parametry lub czynniki, które powodują powstawanie danej wady wypraski i zaproponować ich modyfikację w celu jej usunięcia lub zminimalizowania. Jednak określenie odpowiedniego profilu ustawienia tych parametrów zawsze przeprowadza się wieloetapowo i wymaga bardzo dobrej znajomości właściwości tworzywa, maszyny, formy wtryskowej, przepływu tworzywa, procesu, parametrów i dużej czujności oraz zdolności do obserwacji. Bardzo często też przetwórcy nazbyt ufają w doskonałość zaawansowanych maszyn i ich możliwości oraz często nie biorą pod uwagę faktu błędnej konstrukcji detalu (niedostosowanego do technologii wtryskiwania) lub błędnie skonstruowanej formy wtryskowej, która generuje wiele problemów różnej natury (termicznej, reologicznej, technicznej). Pozostaje pytanie, które zawsze należy sobie zadać czy realizować nowy trudny, ale i obarczony dużym ryzykiem projekt samemu czy przekazać go w ręce partnera z doświadczeniem i to na nim pozostawić odpowiedzialność za wszystkie etapy wdrożenia i produkcji. Każdy musi sam ocenić swój potencjał i możliwości technicznej i doświadczenie.Dr hab. inż. Przemysław POSTAWA, prof. PCz
6 kroków do produkcji Twojego pomysłu
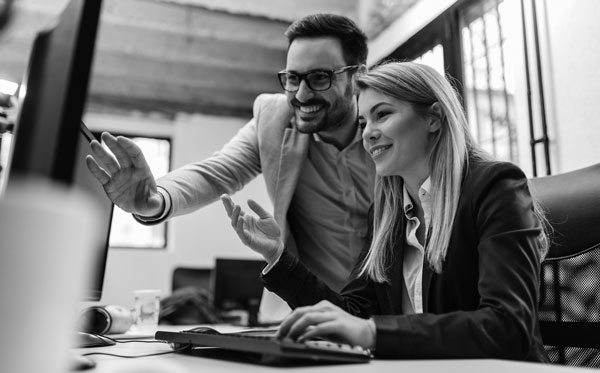
- 1. Design na podstawie wymagań klienta
- 2. Projekt wyrobu 3D - wizualizacja komputerowa
- 3. Prototypowanie i walidacja projektu
- 4. Nadzór nad projektem formy wtryskowej
- 5. Nadzór nad wykonaniem formy wtryskowej
- 6. Produkcja wyrobów z tworzyw sztucznych
Zbieramy od Państwa wszystkie oczekiwania i dane niezbędne do wykonania wstępnego projektu wyrobu. Na tej podstawie powstaje pierwsza wycena produkcji nowego projektu.
Tworzymy projekt 3D w programie, w którym można zweryfikować i dopasować wirtualnie każdy detal wyrobu z tworzywa sztucznego. Na tym etapie jest jeszcze możliwość istotnych zmian konstrukcyjnych.
Po akceptacji wirtualnego wyrobu powstaje prototyp funkcjonalny w technologii prototypowej Jest to decydujący moment w procesie realizacji wyrobu, w którym następuje weryfikacja wstępnych założeń.
Po zaakceptowaniu modelu wypraski i omówieniu podstawowych parametrów formy wtryskowej rozpoczyna się proces konstrukcji formy.
Kolejny etap to wykonanie poszczególnych elementów formy wtryskowej, jej montaż i próby na wtryskarce. Produkcja form oparta jest na materiałach i surowcach renomowanych dostawców, a posiadany przez nas park maszynowy pochodzi od światowych producentów obrabiarek.
Końcowym etapem o strategicznym znaczeniu jest produkcja wtryskowa wyprasek. Realizowana jest w oparciu o wtryskarki Arburg i Krauss Maffei z atestowanych tworzyw światowych producentów.