MEET US
Automated production of plastic products, injection moulding, improvement of technology and development of machinery- these are just a few facts about our company.
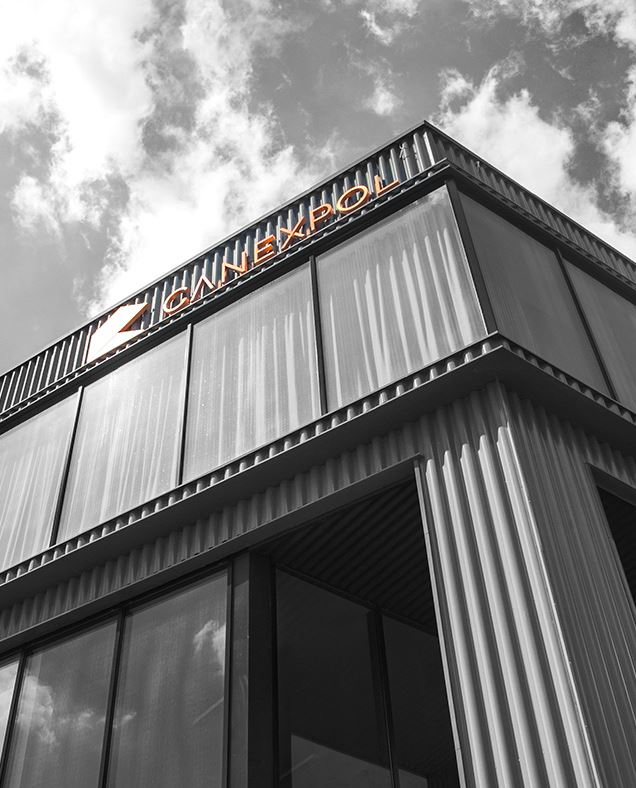
BUILDING ON THE FOUNDATION OF THE TRADITION
Let's go back in time to 1983.It is when January Miensak begins his first production in workshop conditions. Despite many difficulties - he makes his dreams come true. Being a visionary, he pushes another boundaries and establishes Canexpol which just after a few years is a dynamically growing company ahead of the competition.
FROM GENERATION...
To generation. The subsequent generations manage the company following the same path defined by:
- focusing on the customers’ needs
- high standard of work
- reliability
- partnership in cooperation
- good team of experts
- seeking innovative solutions
- exploring the latest technologies and materials
- constant development
- taking care of the environment
We seek and offer innovative solutions, explore the latest technologies and materials. We cooperate with both small and large companies, being committed to such values as stability, mutual respect and honest relationships. Thanks to our production many companies are becoming leaders in their own areas of activity.
Quick video trip
Take a quick trip and see the elements of selected production processes at our company.
products delivered to our customers annually
production, warehouse and office space
experts in Canexpol Team
Our factory
WE ARE READY FOR NEW CHALLENGES::
- We have doubled the company's area
- We currently have a production space with a total area of over 9,000 m2
- Our production is based on the latest technologies
- We have a flexible approach toward each order
- Partnership is our superior principle
- We have a warehouse space with a total area of over 11,000 m2
- Being characterized by quality, we can build stable relationships with our partners
- We analyze each project to find the best solutions together
- We combine modern production with traditional values
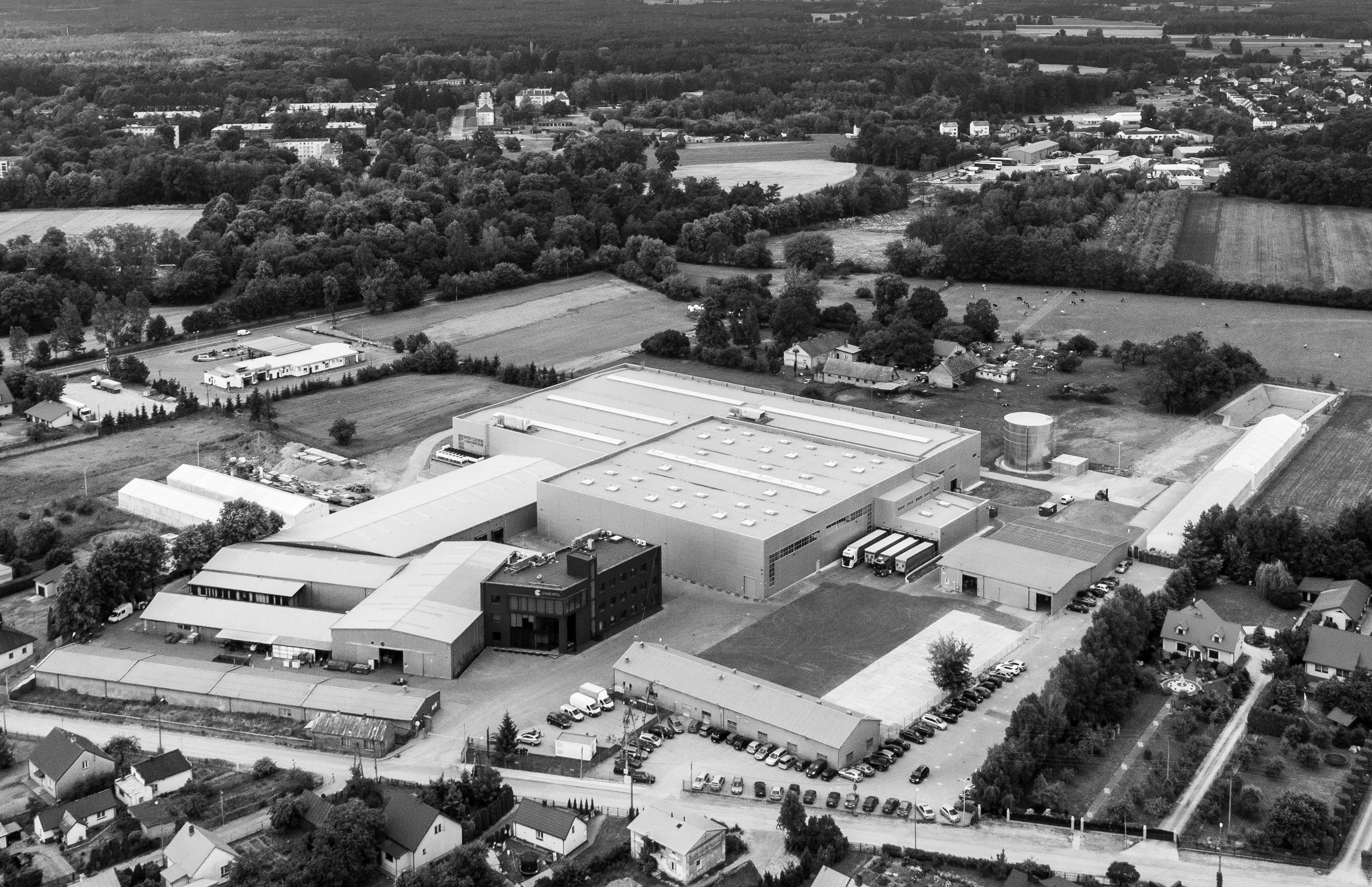
We have modern machinery thanks to which we can realize technologically advanced projects in terms of production from plastic.
The injection moulding plant is equipped with the most modern injection moulding machines of renowned German brands - Arburg and Krauss Maffei - with closing power from 500 to 6 500 tons. The machines are equipped with robots enabling automation of the production processes. At present we have a production area of over 9,000 m2, equipped with state-of-the-art production machinery and equipment.t.
WE ARE ENVIRONMENTALLY FRIENDLY
We take care of the natural environment everyday. We minimize CO2 emission to the atmosphere, and the heating of our facility comes from the recovery of energy generated as a result of the production processes. All plastics used in our plant may be recycled.
- We have reduced electricity consumption thanks to energy efficient LED lighting systems with motion detectors.
- Our products may be recycled.
- We have optimized our production lines in terms of electricity consumption.
- We eliminate disposable packaging thanks to reusable dishes and reverse osmosis system.
How do we work?
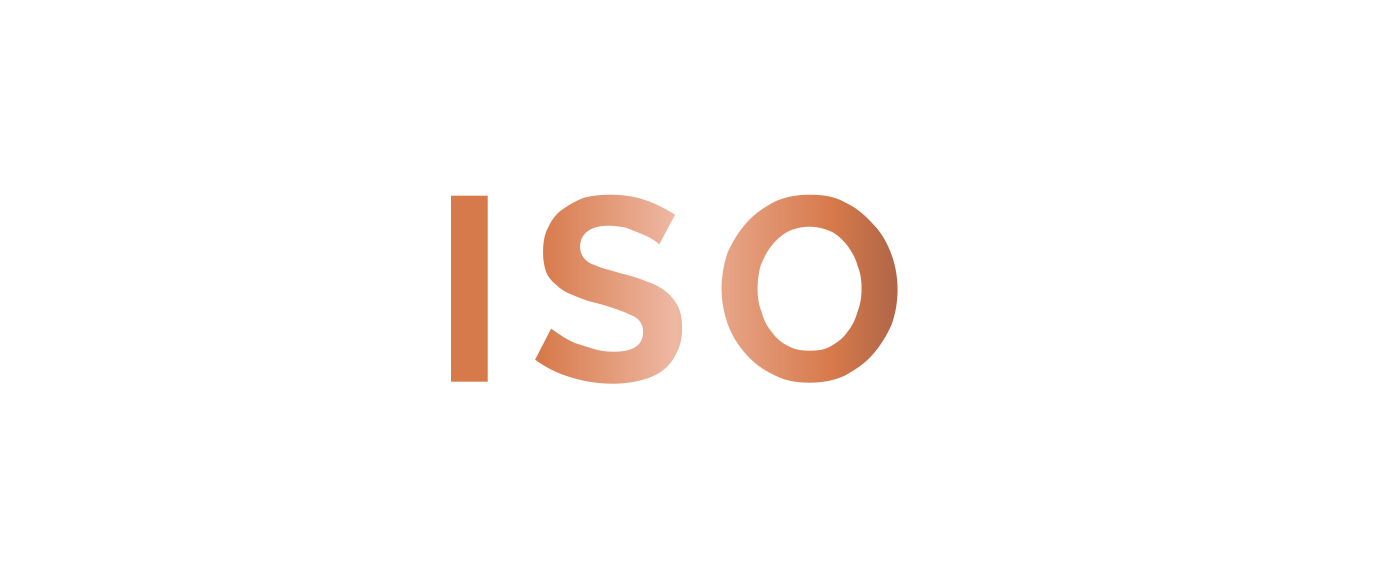
The Quality Management System compliant with the PN-EN ISO 9001:2015 standard is aimed at ensuring the fulfilment of customer requirements and constant improvement of the quality of manufactured products or provided services. It enables us to conduct functional and effective business operations that allow us to maintain our market position and adapt to changing market conditions.
The process approach used in formulating, implementation and improvement of the quality management system expedites the circulation of information and documents in our company and introduces a precise division of tasks, authorisations and responsibilities for all employees. All this facilitates the constant improvement of the quality of customer service, which directly translates into an increase in satisfaction.
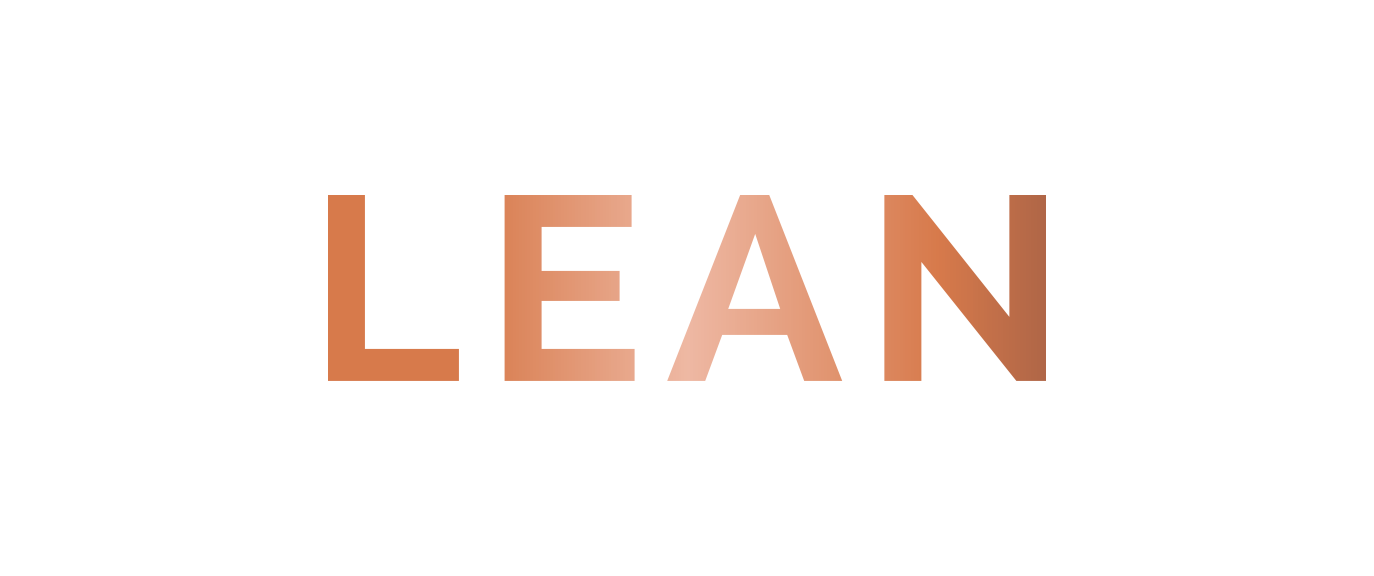
As a part of Lean concept, we are continuously developing a organizational culture aimed at constant growth allowing to reach defined business goals and solve problems effectively. Within Lean concept we undertake activities aimed at (among others):
- Identification of process losses (value stream mapping);
- standardization and optimization of production and business processes (eliminating activities that do not add value in the realized processes);
- system problem solving based on PDCA cycle;
- optimization of information flow and process stability (implementation of visual management tools);
- optimization of work stand organization (5S);
- increase of the use of machines and equipment expressed in OEE (TPM system implementation);
- constant development of our employees by numerous trainings.
We believe that thanks do the active implementation of Lean concept, internal need for improvement and engagement of all employees, we will be able to satisfy the expectations of our customers, providing them in a timely manner with products and services of expected quality, price.